ADMINISTRATIVE POLICY
Executive Director of Enviromental Health and Safety
Policy Statement
It is the policy of Tulane University to protect employees from respiratory hazards in a manner that is consistent with the regulations promulgated by the Occupational Health and Safety Administration (OSHA) as a result of working with harmful dusts, fumes, gases, vapors, and other hazardous airborne substances. Tulane University supports and will strive to meet or exceed the OSHA Standard requirements in Title 29 of the Code of Federal Regulation Part 1910 (29 CFR 1910.134) and similar initiatives.
Purpose and Scope
The purpose of this policy is to support the protection of Tulane University employees from respiratory hazards, injuries, and illnesses, and to promote respiratory safety in accordance with the OSHA Respiratory Protection Standard, 29 CFR 1910.134. Protection from respiratory hazards are first accomplished by engineering and work practice control measures. When engineering or work practice controls are not feasible or while controls are being implemented and/or evaluated, respiratory protection may be required. This policy establishes procedures and details the safe use of respiratory protection equipment.
This policy applies to Tulane University employees who use respiratory protection. Respiratory protection shall be provided whenever such equipment is necessary to protect the health or provide for the comfort of University employees. This policy shall apply University-wide and shall include all situations where respiratory protection is required against the inhalation of hazardous material. Protection shall be used:
- When effective engineering controls are not feasible;
- During emergencies;
- For certain maintenance operations;
- While controls are being instituted;
- When indicated by the Safety Data Sheet for a given chemical; or
- If ambient concentrations of toxic or hazardous materials exceed permissible exposure limits or threshold limit values.
Employees that work with Hazardous Biological Agents are subject to requirements of the Biosafety Manual 2018 developed by the Tulane Office of Biosafety. The requirements set forth in the Biosafety Manual 2018 and the TNPRC Biosafety Manual shall take precedent to this policy.
Applicability of this Policy
This policy applies to any individual that is hired by Tulane University to perform a service for wages, salary, or any form of compensation.
Website Address
Contacts
Definitions
Air-purifying respirator - A respirator with an air-purifying filter, cartridge, or canister that removes specific air contaminants by passing ambient air through the air-purifying element.
Atmosphere-supplying respirator - A respirator that supplies the respirator user with breathing air from a source independent of the ambient atmosphere and includes supplied-air respirators (SARs) and self-contained breathing apparatus (SCBA) units.
Emergency situation - Any occurrence such as, but not limited to, equipment failure, rupture of containers, or failure of control equipment that may or does result in an uncontrolled significant release of an airborne contaminant.
Employee - A person employed for wages, salary, or compensation. This includes any person and/or graduate student who receives a stipend or compensation from Tulane University in any form, which can include but is not limited to salary, benefits, stipends, or tuition waivers.
Employee exposure - Exposure to a concentration of an airborne contaminant that would occur if the employee were not using respiratory protection.
Escape-only respirator - A respirator intended to be used only for emergency exit.
Filtering face-piece (dust mask) - A negative pressure respirator with a filter as an integral part of the face-piece or with the entire face-piece composed of the filtering medium.
Fit factor - A quantitative estimate of the fit of a particular respirator to a specific individual, and typically estimates the ratio of the concentration of a substance in ambient air to its concentration inside the respirator when worn.
Fit test - The use of a protocol to qualitatively or quantitatively evaluate the fit of a respirator on an individual. (See also Qualitative fit test and Quantitative fit test.)
High efficiency particulate air (HEPA) filter - A filter that is at least 99.97% efficient in removing monodisperse particles of 0.3 micrometers in diameter. The equivalent National Institute for Occupational Safety and Health Title 42 of the Code of Federal Regulations, Part 84 particulate filters are the N100, R100, and P100 filters.
Immediately dangerous to life or health (IDLH) - An atmosphere that poses an immediate threat to life, would cause irreversible adverse health effects, or would impair an individual's ability to escape from a dangerous atmosphere.
Loose-fitting face piece - A respiratory inlet covering that is designed to form a partial seal with the face.
Negative pressure respirator (tight fitting) - A respirator in which the air pressure inside the face piece is negative during inhalation with respect to the ambient air pressure outside the respirator.
Occupational Exposure Limit - An upper limit on the acceptable concentration of a hazardous substance in workplace air for a particular contaminant or class of contaminant.
Oxygen deficient atmosphere - An atmosphere with an oxygen content below 19.5% by volume.
Physician or other licensed health care professional (PLHCP) - An individual whose legally permitted scope of practice (i.e., license, registration, or certification) allows him or her to independently provide, or be delegated the responsibility to provide, some or all of the health care services required by this policy.
Positive pressure respirator - A respirator in which the pressure inside the respiratory inlet covering exceeds the ambient air pressure outside the respirator.
Powered air-purifying respirator (PAPR) - An air-purifying respirator that uses a blower to force the ambient air through air-purifying elements to the inlet covering.
Qualitative fit test (QLFT) - A pass/fail fit test to assess the adequacy of respirator fit that relies on the individual's response to the test agent.
Quantitative fit test (QNFT) - An assessment of the adequacy of respirator fit by numerically measuring the amount of leakage into the respirator.
Respiratory inlet covering - The portion of a respirator that forms the protective barrier between the user's respiratory tract and an air purifying device or breathing air source, or both. It may be a face piece, helmet, hood, suit, or a mouthpiece respirator with nose clamp.
Self-contained breathing apparatus (SCBA) - An atmosphere-supplying respirator for which the breathing air source is designed to be carried by the user.
Service life - The period of time that a respirator, filter or sorbent, or other respiratory equipment provides adequate protection to the wearer.
Supplied-air respirator (SAR) or airline respirator - An atmosphere-supplying respirator for which the source of breathing air is not designed to be carried by the user.
Tight-fitting face piece - A respiratory inlet covering that forms a complete seal with the face.
User seal check - An action conducted by the respirator user to determine if the respirator is properly seated to the face.
Unit - A department, section, center, or program, or any number or configuration of these components.
Policy and Procedures
8.1 Responsibilities
8.1.1. Office of Environmental Health and Safety (OEHS)
- Designate an employee of OEHS as the Respiratory Protection Program Administrator.
- Develop a written university-wide respiratory protection program.
- Provide overall administrative and technical support for establishing and monitoring this program.
- Evaluate potential hazardous operations, when requested, and identifies employees who are required to use respirators.
- Recommend the appropriate type of respiratory protection based upon the hazard.
- Ensure respirator assessments and required evaluations are conducted
- Provide training in the selection, limitations, fit-testing, use, care and maintenance, of
- respirators which are issued to employees. All respirator uses shall receive initial and annual training, fit test, and medical clearance.
- Coordinate with the Manager of the Office of Occupational Healthcare Surveillance to ensure that potential respiratory hazards are identified, and all employees that are required to use respirators are physically evaluated and fit tested annually.
- Inform managers and supervisors in writing of operations which require the use of respirators.
- Maintain records of designated respirator users and operations which require respiratory protection.
- Provide training to employees who perform respiratory fit tests.
- Perform qualitative of quantitative respirator fit test in accordance with Appendix A of 29 CFR 1910.134 and this policy.
- Retain and distribute fit test documentation.
- Periodically evaluate this program’s effectiveness and update this policy and applicable procedures.
8.1.2. Units, Department Heads/Directors, Principal Investigators, And/or Supervisors
- Ensure employees under their supervision who are required to use respiratory protection attend scheduled medical appointments, fit tests, and Respiratory Protection Training.
- Ensure employees under their supervision comply with this policy, training, and regulations.
- Aid OEHS with identification and assessments of the respiratory hazard(s) in their work areas based upon specific activities and/or workplace conditions.
- Ensure adequate supply of respirators, spare parts, cartridges/filters and supplies needed to clean and maintain respiratory protection equipment.
- If using third party medical provider, bear the cost of all medical evaluations, examinations, and fit testing for University employees who wear respirators.
- Notify OEHS and the Manager of the Office of Occupational Healthcare Surveillance of employees who are assigned tasks that require the use of respiratory protection.
- Comply with this policy. Each supervisor/principal investigator shall be responsible for the administration and enforcement of the respiratory protection program for employees under their supervision.
- Notify the OEHS immediately of known violations or when contacted by a regulatory agency regarding this policy.
8.1.3. Employees Required to Wear Respirators
- Comply with this policy, training, and regulations.
- Use respiratory equipment in accordance with the training and instructions they received.
- Use only approved respiratory protection equipment in which the employee has been
- properly training, medically qualified and fit tested.
- Inspect respiratory protection equipment prior to use for proper function and condition
- Conduct a negative and positive pressure seal check when donning respirators to ensure
- adequate face to facepiece seal.
- Properly maintain, clean (in accordance with Appendix B-2 to 40 CFR 1910.134 and
- manufacturer’s guidelines), and store respiratory protection equipment.
- Report for all scheduled medical exams, fit tests, and training.
8.1.4. Tulane Living Well Occupational Health Clinic or Tulane National Primate Research Center Occupational Health Clinic (TNPRCOH)
- Administer the medical questionnaire provided in Appendix C of 29 CFR 1910.134 or an initial medical examination that provides the same information as the OSHA medical questionnaire.
- Perform appropriate medical exams to ensure the employee is qualified to wear respiratory protection equipment.
- Provide written medical recommendation to the employee regarding the employee’s ability to use the respirator.
- Provide or refer additional medical evaluations if deemed necessary.
- Perform qualitative of quantitative respirator fit test in accordance with Appendix A of 29.
- CFR 1910.134 and this procedure.
- Provide medical evaluations to employees in event of an inhalation exposure event
- Retain and distribute fit test documentation.
8.1.5. Office Of Occupational Healthcare Surveillance
- Schedule and coordinate respirator training and fit testing with employees.
- Coordinates with the Office of Environmental Health and Safety to ensure that employees exposed to respiratory hazards are included in the respiratory protection program.
- Maintain records of medical evaluations and fit test records in accordance to this procedure, 29 CFR 1910.134, and 29 CFR 1910.1020.
8.2 Respirator Selection Criteria
- Respirators approved by the National Institute for Occupational Safety and Health (NIOSH) shall be used at Tulane University.
- Respirator selection is dependent upon a hazard assessment conducted by the Office of Environmental Health and Safety and/or with assistance from individual departments in which the hazard is present.
- Hazard assessments includes the following information:
o The toxic substance(s) or hazard(s) present in the work environment;
o Significant properties and effects of the hazard(s) present;
▪ (The type of air contaminant including the physical and chemical properties, toxicity, physiological effects, and concentration)
o Determine all significant factors associated with the job and the nature of the job operation or process that may affect the respirator’s performance;
o Identify the location of the hazardous area;
o Determine the period and/or conditions for which respiratory protection will be required;
o Identify the functional and physical characteristics of the respirator needed and define its acceptable limitations;
o Determine what facilities and personnel are needed for respirator storage and maintenance.
8.3 Medical Evaluation
A medical evaluation to determine the ability for an employee to use respiratory protection is required prior to use of respiratory protection equipment and annually thereafter.
The medical evaluation will include a baseline medical examination, medical history, and a review of the employee’s work history.
The Tulane Living Well Occupational Health Clinic shall conduct the medical evaluation for Tulane University employees.
The Tulane Living Well Occupational Health Clinic shall issue a written medical assessment for each employee examined evaluating the employee’s ability to safely use the assigned respirator.
The Tulane Living Well Group Occupational Health Clinic will schedule and conduct annual medical surveillance examinations for those employee’s included in the respiratory protection program.
8.4 Training
All employees who are required to use respirators will be trained annually in the following aspects of respiratory protection:
- The purpose of respiratory protection;
- The nature, extent and effects of respiratory hazards in the workplace;
- The use and limitations of respiratory protection being used;
- Instructions for inspecting and donning the respirator;
- Types of fit tests;
- Maintenance and storage of the respirator;
- Instructions on emergency procedures;
- Requirements of this procedure and 29 CFR 1910.134.
8.5 Fit Testing
Respirator fit test are provided by the Tulane Living Well Occupational Health Clinic or OEHS after the employee has received medical clearance and has completed respiratory protection training. Employees must receive medical clearance, training and fit testing annually.
Quantitative and Qualitative fit testing shall be performed in accordance with the requirements specified by the OSHA Respiratory Protection Standard, 29 CFR 1910.134 Appendix A.
Quantitative Fit Testing shall be performed is accordance with the quantitative fit test apparatus operator’s manual.
The results of a quantitative fit test shall indicate “pass” or “fail” result based upon the fit factor calculated by the apparatus. Filtering facepiece respirators and half mask tight fitting respirators shall demonstrate a minimum fit factor of 100 to “pass.” Full-face respirators shall demonstrate a minimum fit factor of 500 to “pass.”
Fit test reports shall contain at minimum:
- The name or identification of the employee;
- Type of fit test performed;
- Specific make, model, style, and size of respirator tested;
- Date of test;
- The pass/fail results for qualitative fit test or the fit factor and test results for quantitative fit test.
Fit test reports shall be kept for a minimum of three years by the Tulane University Medical Group Occupational Health Clinic. Copies of fit test reports shall be sent to the OEHS at OEHS@tulane.edu on a monthly basis.
8.6 Maintenance, Inspection, and Storage
Employees are responsible for cleaning and sanitizing their issued respirator prior to use and following each usage. All cleaning and sanitizing practices dictated in this policy shall be performed in accordance with Appendix B-2 to 40 CFR 1910.134 and manufacturer’s guidelines.
Units, department heads/directors, principal investigators, and/or supervisors shall ensure adequate supplies of respirators, spare parts, cartridges/filters, and any additional supplies needed to properly clean and maintain respirators.
Respirators that are shared between employees shall be properly cleaned and sanitized prior to being worn by different individuals.
Filtering facepiece respirators, such as N95 respirators, shall not be shared between employees.
Employees shall inspect the respirator prior to each use.
Respirators intended for emergency use shall be cleaned and sanitized after each use.
Respirators must be stored in areas to protect them from damage and which are free from hazards.
8.7 Routine Use
A list of approved respirators for use at Tulane University is listed in Appendix A.
Routine tasks and operations that require the use of respiratory protection is outlined in Appendix B
OEHS will inform supervisors in writing of any additional tasks, once identified, which require respiratory protection. Appendix B shall be updated as necessary.
Respirator cartridge change out schedules shall be determined using the math model developed by NIOSH to calculate breakthrough times for various chemicals. The established change out schedule for approved respiratory protection cartridges is provided in Appendix C.
8.8 Emergency Use
Employees of Tulane University are not permitted to enter spaces that are considered Immediately Dangerous to Life and Health (IDLH).
Emergency situations that require entering IDLH atmospheres shall be accessed by the New Orleans Fire Department or other emergency response entities.
8.9 Voluntary Usage
Filtering face-piece respirators are permitted to be used on a voluntary basis in situations that have been determined not to require respiratory protection and the use of filtering face-piece respirators do not create a hazard.
All employees voluntarily wearing filtering face-piece respirators shall be provided with a copy of Appendix D of 29 CFR 1910.134 by OEHS. The respirator is not allowed to be worn in atmospheres containing contaminants for which the respirator is not designed to protect against.
The user of the voluntary use respirator must read and heed all instructions provided by the manufacturer on the use, maintenance, cleaning and care, and warning regarding respirator limitations.
8.10 Program Evaluation
The respiratory protection program shall be reviewed annually based on the following criteria:
- Review of employee exposure assessment information;
- Review of the written program;
- Consulting with respirator users;
- Review of prior respirator selections;
- Performing workplace inspections for respirator use, storage, and maintenance;
- Observing respirator use in the field;
- Compliance with OSHA regulations and this policy;
- Performing a review of the respiratory protection training content;
- Performing an audit of required training.
8.11. Recordkeeping
8.11.1. Document Generation
The following documents are generated by this program:
- Medical qualification to wear respiratory protection
- Quantitative or Qualitative fit test reports.
- Respirator users database.
8.11.2. Medical Qualifications
- The Tulane Living Well Occupational Health Clinic or TNPRCOH shall keep all medical evaluations conducted to determine a user’s ability to wear respiratory protection for the duration of employment plus 30 years.
- Records of medical evaluations required by this policy and OSHA 29 CFR 1910.134 shall include:
o Name and Splash ID of employee; and
o Physicians written opinion.
8.11.3. Fit Test Reports
- OEHS and Tulane Living Well Occupational Health Clinic shall retain respirator fit test reports for three years at minimum. The fit tester shall save all fit test reports to S:\Respiratory Protection\Fit Testing.
- Fit test reports shall contain the following information:
o Fit test protocol performed;
o Make, model, style, and size of respirator;
o Date of fit test;
o Name and Splash ID of employee being fitted;
o Pass/fail results for qualitative fit tests;
o Fit factor for quantitative fit tests.
8.11.4. Respirator Users Database
Respirator users database shall include the following information:
- Employees first and last name;
- Make, model, style, and size of respirator;
- Medical clearance date;
- Fit test date;
- Employee's department;
- Hazardous operation for respirator use
8.11.5. Record Availability
Documents generated according to this policy shall be made available to applicable employees per request.
8.12. Referenced Regulations
- Occupational Safety and Health Administration, 29 CFR 1910.134, General Industry Standard for Respiratory Protection
- National Institute for Occupational Safety and Health Respirator Certification Standard, 42
- CFR Part 84, Occupational Safety and Health Administration, 29 CFR 1910.1020, Access to Employee Exposure and Medical Records
- Tulane University Office of Biosafety, Biosafety Manual 2018. https://tulane.app.box.com/s/jpv7j3awyephg18wzocgxlq2u422tkxi
- Tulane University Office of Biosafety, TNPRC Select Agent Biosafety Manual
Consequence of Violating the Policy
Violation of this policy may result in disciplinary action, up to and including termination. For consequences of violating the policy refer to the Faculty and Staff handbooks found at policy.tulane.edu
Approved Respirators for Use at Tulane University
Routine Task and Operations Requiring Respiratory Protection
Respirator Cartridges Change-Out Schedule
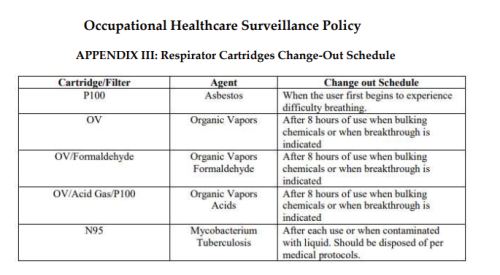