ADMINISTRATIVE POLICY
Executive Director of Environmental Health & Safety
Policy Statement
It is the policy of Tulane University to classify, inform, and communicate the hazards associated with the use of potentially hazardous chemicals to its employees. Employees working with hazardous chemicals need to know the identity of each chemical, the associated hazards, and how to protect themselves.
Purpose and Scope
The purpose of the Hazard Communication Plan (HCP) is to ensure that the hazards of all chemicals produced or imported are classified, and that information concerning the classified hazards is transmitted to Tulane University personnel. Requirements of the HCP are intended to be consistent with the provisions of the United Nations Globally Harmonized System of Classification and Labelling of Chemicals (GHS), Revision 3. The transmittal of information is to be accomplished by means of comprehensive hazard communication plan, which is to include container labeling and other forms of warning, safety data sheets and employee training.
The Hazard Communication Plan (HCP) set forth fulfills the Occupational Safety and Health Administration’s (OSHA) requirement for a “written” hazard communication plan, described in 29 CFR 1910.1200, is designed to address the needs of employees working with hazardous chemicals. This HCP also fulfills requirements of the Environmental Protection Agency’s Emergency Planning and Community Right-to-Know Act (EPCRA) described in 42 CFR 116 and the Department of Homeland Security’s Chemical Facility Anti-Terrorism Standards (CFATs).
The scope of the HCP includes:
- Hazard evaluation and classification,
- Hazardous chemicals inventory,
- Hazardous chemical container labeling policy,
- Safety data sheet (SDS) policy,
- Information and training curriculum for handling hazardous materials,
- The methods of informing contractors of hazards to which their employees may be exposed,
- Sealed containers,
- Laboratory standards, and
- Trade secrets.
Applicability of this Policy
This policy applies to Tulane University personnel who use or come into contact with chemicals under normal working conditions of use or in a foreseeable emergency. If a worker only encounters chemicals in non-routine, isolated instances, and is not exposed to hazardous chemicals under normal operating conditions or in foreseeable emergencies, the worker is exempt from requirement of the HCP. The department’s supervisory personnel shall make the determination as to whether or not workers are exempt under the standard. If the department requires assistance in the determination, the supervisor should contact the Office of Environmental Health & Safety (OEHS) for guidance.
Website Address
Contacts
Definitions
Authorized person - Any person required by work duties to be present in regulated areas or authorized to do so by the employer.
Emergency - Any occurrence, such as but not limited to equipment failure, rupture of containers, or failure of control equipment that result in an uncontrolled release of a significant amount of formaldehyde.
Work area - A room or area where hazardous chemicals are used and where employees are present.
Laboratories - A room or area where chemicals are utilized in normal working activities; besides scientific labs, may also include select shops, art studios, facilities, or physical plant locations.
Policy and Procedures
8.1 Responsibilities
Success in implementing the Hazard Communication Plan depends on the cooperation of employees who have been identified as working with hazardous chemicals.
8.1.1. Office of Environmental Health and Safety (OEHS)
Assist Unit/Department Heads, Principal Investigators and Directors in determining potential chemical hazards in their respective work environments.
- Work with Department Safety Representatives (DSRs) to improve laboratory work practices.
- Provide training to employees on chemical hazards, PPE, and proper work practices.
- Certify environmental health and safety compliance for grant proposals prior to funding. The Director of EOHS shall not certify a grant if the applicant is not in compliance with policies related to any of the following topics: OSHA HCP, OSHA Laboratory Standard, Animal Handling Health Surveillance Program, Fire Safety, Radiation Safety, Hazardous Materials and Waste, and Biosafety.
8.1.2. Unit/Department Heads, Principal Investigators, and/or Directors
- At all times, maintain a chemical inventory of materials being utilized or stored in all work areas and maintain records.
- Ensure employees working in the areas under their supervision are provided the information and training protect their health and the work environment, including proper work practices.
- Cover the cost of any prescribed personal protective equipment (PPE) and/or engineering controls.
- Establish and maintain regulated areas at the direction of OEHS including limiting access to regulated areas to authorized persons who have been trained to recognize the hazards associated.
- Inform any contract labor working in or around regulated areas of the access restrictions and locations.
- Institute appropriate engineering and work practice controls to reduce and maintain exposures to chemical hazards via Standard Operating Procedures (SOPs).
8.1.3. Departmental Safety Representatives (DSR)
- Ensure that the units they represent are in compliance with regulatory standards and with the University HCP set forth in this section.
- DSRs collect and submit to OEHS required documentation such as inspection reports, training documentation, chemical inventories, etc., prepared by supervisors and principal investigators.
- Ensure that the necessary measures have been taken by supervisory and other unit personnel to correct problems discovered during unit inspections. If corrections are not made despite deadlines and warnings from the DSR, the DSR shall report the unit's non-compliance to the Unit Head.
8.1.4. Employees
- Comply with requirements of HCP.
- Be alert to potential hazards of all materials in their work areas by consulting labels, SDS's, and following established work practices to protect their health and work environment.
- Properly use engineering controls and wear PPE as required.
- Complete training as required.
8.2 Hazard Evaluation & Classification
8.2.1. Manufacturer/Importer Evaluation
Chemical manufacturers and importers shall evaluate chemicals produced in their workplaces or imported by them to classify the chemicals in accordance with this section. For each chemical, the chemical manufacturer or importer shall determine the hazard classes, and, where appropriate, the category of each class that apply to the chemical being classified. Employers are not required to classify chemicals unless they choose not to rely on the classification performed by the chemical manufacturer or importer for the chemical to satisfy this requirement. The University shall rely on the evaluations performed by the manufacturer/importer. The following sources are used by manufacturers/importers in evaluating the hazards of their products:
- Substances listed in OSHA 29 CFR 1910, Subpart Z, “Toxic and Hazardous Substances.”
- Threshold Limit Values for Chemical Substances and Physical Agents in the Work Environment published by the American Conference of Governmental Industrial Hygienists (ACGIH).
- Annual Report on Carcinogens published by the National Toxicology Program (NTP).
- Monographs published by the International Agency for Research on Cancer (IARC).
- All chemicals listed as hazardous by the EPA Superfund Amendments Reauthorization Act (SARA), Resource Conservation and Recovery Act (RCRA) regulations, and the State of Louisiana Hazardous Materials Information Development, Preparedness and Response Act.
- Any human epidemiological study, individual case report or animal toxicological testing which indicates that a material presents a health hazard, provided that the study indicates an adverse health effect that is likely to occur, that the results are statistically significant, and that the study was conducted in accordance with scientific principles.
8.2.2. Safety Data Sheets (SDS)
If a chemical is determined to be hazardous, the manufacturer or distributor must document the results of the chemical evaluation on a Safety Data Sheet (SDS) that meets OSHA information requirements and be consistent with the provision of the United Nations Globally Harmonized System of Classification and Labelling of Chemicals (GHS).
If any of the required information is missing, the evaluation shall be deemed inadequate and the product user or OEHS shall undertake measures to obtain an acceptable SDS from the manufacturer or distributor. If an acceptable SDS is not obtained, use of the product shall be discontinued at the University. The purchaser or OEHS shall inform the Purchasing Department and will discontinue use and further orders of the product. All units shall be notified that purchase orders, as well as standing orders, for this product will not be processed.
8.2.3. Objection to Use of Manufacturer/Importer Chemical Evaluation
If a Tulane employee chooses not to rely on the chemical evaluation provided by the manufacturer or importer, that employee must contact OEHS in writing, stating his/her objections to the manufacturer's or importer's determination, and the methods and/or sources the employee intends to use in evaluating the chemical. Approval of written individual hazard determinations shall be issued by OEHS only after review of both the employee’s objections to the manufacturer/importer evaluation and the employee’s alternative methods of evaluation, and consultation with persons responsible for the affected area.
8.2.4. EPA Reporting
For any quantity of chemicals which trigger inventory reporting (500 pounds of a chemical present on site on any one day during the preceding calendar year or some extremely hazardous substances with lower threshold quantities as listed on the Louisiana State Police website), the University must provide a Tier II form to the Louisiana State Police (LSP), Hazardous Materials Unit by March 1 of the following year. Inventory forms must include a list of the chemicals, the hazard categories, inventory ranges, and storage conditions and locations, and must be filed with the Louisiana Emergency Response Commission (LERC), the Local Emergency Planning Committee (LEPC), and the local fire department. E-filing is available on the LSP website.
8.3 Hazardous Chemicals Inventory
Every chemical or material known to be present in a work area must be listed as part of the University’s chemicals inventory unless the material is exempt. OEHS shall maintain a Hazardous Chemicals Reporting List.
Tulane University shall report to regulatory agencies any hazardous chemicals that are stored in quantities of the threshold planning quantity or 500 pounds, whichever is greater. Threshold planning quantities vary based on the hazard severity of the chemical. Chemical storage quantities triggering EPCRA reporting requirements is submitted electronically through the Tier II Report to the Louisiana State Police and the Local Emergency Planning Committee (LEPC). A hard copy will be mailed to the local fire departments. Tier II Reports require not only the list of chemicals and respective quantities, but the hazard categories, storage conditions and locations. Chemical storage quantities triggering CFATs reporting requirements will be individually filed as chemicals of interest with the Department of Homeland Security (DHS).
The Hazardous Chemicals Reporting List is maintained by OEHS and shall be distributed on an annual basis to responsible personnel. Unit/Department Heads, Principal Investigators, and/or Directors are to evaluate the Hazardous Chemicals Reporting List to determine if any hazardous chemicals are to be provided to OEHS for reporting purposes. For each hazardous chemical reported, Unit/Department Heads, Principal Investigators, and/or Directors are to provide the total quantity being stored in the work area and the location of storage. Total quantities are to be reported in pounds by converting from the total volume.
As stated in Section 8.1.2 of Responsibilities, Unit/Department Heads, Principal Investigators, and/or Directors are to maintain an inventory of chemicals and/or substances utilized in their respective work areas. These inventories shall be used as a reference tool for review of the Hazardous Chemicals Reporting List.
8.3.1. Factors and Requirements for Inventory Preparation
OEHS requires that the chemical inventory for each location where hazardous chemicals are used, stored, or handled, shall be annually updated by supervisors/principal investigators. If a new chemical posing an extreme hazard is added during the year, or a significant quantity of a hazardous chemical is added to the inventory during the year, more frequent updating may be required. Contact OEHS with this type of additional information or with questions.
The identity of any substance appearing on the chemical inventory shall be the same name that appears on the manufacturer's label, in-house label, and the SDS for that substance.
Each work area must keep a current copy of its specific chemical inventory and/or have ready access to an SDS for each listed chemical.
8.3.2. Exempt Materials
The following materials are exempt from the Hazard Communication Standard and need not be included on the chemical inventory:
- Hazardous waste, as defined by the Solid Waste Disposal Act and the Resource Conservation and Recovery Act and regulated by the EPA,
- Any hazardous substance defined by the Comprehensive Environmental Response, Compensation, and Liability Act and regulated by the EPA,
- Tobacco and tobacco products,
- Wood and wood products, including lumber that will not be processed, where the chemical manufacturer can establish that the only hazard the materials pose to employees is the potential for flammability or combustibility. Wood or wood products that have been treated with a hazardous chemical are covered by this standard, and wood that may be subsequently sawed or cut, generating dust, is not exempted,
- Articles (any manufactured item other than a fluid or particle that is formed to a specific shape or design during manufacture) that have end use functions dependent in whole or in part upon their shape or design during end use, and that under normal conditions of use do not release more than very small quantities (minute or trace amounts) of hazardous chemical and do not pose a physical or health risk to employees),
- Food or alcoholic beverages sold, used, or prepared in a retail establishment and foods intended for personal consumption by employees while in the workplace,
- Any drug defined in the federal Food, Drug, and Cosmetic Act when it is in solid form for direct administration to a patient (e.g., tablets or pills), drugs that are packaged by the chemical manufacturer for sale to consumers in a retail establishment (e.g., over-the-counter drugs), and drugs intended for personal consumption by employees while in the workplace (e.g., first aid supplies),
- Cosmetics that are packaged for sale to consumers in a retail establishment, and cosmetics intended for personal consumption by employees while in the workplace,
- Any consumer product or hazardous substance defined in the Consumer Product Safety Act and federal Hazardous Substances Act that is used in the workplace for the purpose intended by the chemical manufacturer, and for which the duration and frequency of exposure are not greater than that experienced by consumers when the product or substance is used for purposes intended,
- Nuisance particulates where the chemical manufacturer can establish that they do not pose any physical or health hazard,
- Ionizing and nonionizing radiation, and
- Biological hazards.
8.4 Labeling
8.4.1. Label Requirements
Hazardous chemicals shall not be accepted for use in the University or shipped to any location unless tagged, labeled, or marked in accordance with the Globally Harmonized System (GHS) with at least the following information:
- Product Identifier - common, trade, or chemical name
- Signal word- used to identify particularly hazardous substances, "DANGER" or "WARNING."
- Hazard statement- brief statement of hazardous effects of the chemicals such as "flammable," "causes lung damage," etc.
- Pictogram(s) - used to symbolize the hazard of the chemical or product name, see below.
- Name, address, and telephone number of the chemical manufacturer, importer, or responsible party.
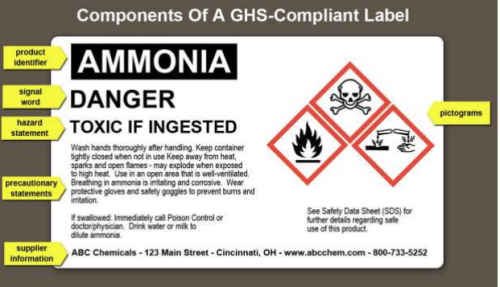
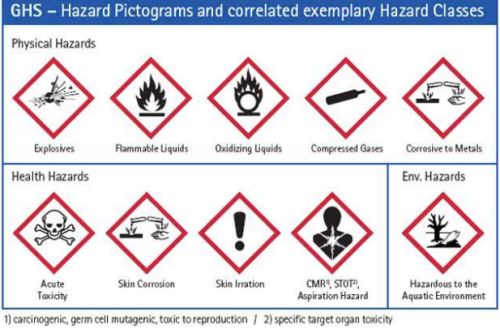
Whenever significant new information regarding the hazards of a chemical becomes available that would entail a changing in the hazard warning component of the label, the new information must be added to manufacturer labels and in-house labels within three months and must be contained on the label of all future shipments into the university. Supervisory personnel shall be responsible for ensuring that the new information is added to all applicable labels. OEHS shall alert deans, directors, and unit heads whenever it becomes aware of such changes, if applicable.
Signs, placards, process sheets, batch tickets, operating procedures, or other such written materials may be used in lieu of affixing labels to individual stationary process containers, as long as the alternative method identifies the container to which it is applicable and conveys the information required by this section to be on a label. The supervisor/principal investigator shall ensure that written materials shall be readily accessible to employees in their work area throughout each shift. Workplace labels or other forms of writing must be legible, in English, and prominently displayed on the container, or readily available in the work area throughout each work shift. Employees who speak other languages may add the information in their language to the materials presented, as long as the information is presented in English as well.
If the hazardous chemical is regulated by OSHA in a substance-specific health standard (example: formaldehyde, benzene), then the label used must be in accordance with the requirements of that standard. OEHS may be contacted for a current list of these substances.
8.4.2. Portable Containers
Labels need not be placed on portable containers into which hazardous chemicals are transferred from manufacturer labeled containers, and which are intended only for the immediate use of the employee who performs the transfer. However, labeling the portable container appropriately can help prevent the accidental misuse of the material by others and is therefore encouraged.
Any portable container of hazardous chemicals not intended for immediate use must be labeled with an appropriate in-house label containing the information specified above.
Supervisory personnel and employees labeling portable containers are jointly responsible for reviewing in-house labels to ensure that the label information is accurate and for determining whether the label conveys the appropriate hazard warnings. OEHS is available to answer any questions that may arise during the course of this review. SDSs and original container labels should be consulted for hazard information when preparing in-house labeling for portable containers. Abbreviations and acronyms should be avoided.
For the purposes of this section, drugs which are dispensed by a pharmacy to a health care provider for direct administration to a patient are exempted from labeling.
8.4.3. Pipes/Piping Systems
Labels need not be placed on pipes or piping systems. However, any chemical hazards associated with an unlabeled pipe/piping system must be communicated to employees who work in the area containing the pipe/piping system. This is the responsibility of the person or unit maintaining or using the pipe/piping system.
8.4.4. Defacing/Removing Labels
A label is not to be defaced or removed unless the container is immediately re-labeled with new information (in compliance with labeling requirements), or unless the container is empty. No employee shall remove any label unless specifically directed to do so by his/her supervisor/principal investigator. Any non-empty container without a label, other than portable containers for immediate use, shall be reported immediately to the work area supervisor/principal investigator. Labels that are hard to read or are coming off of a chemical container must be replaced with an in-house label meeting the requirements listed above.
8.4.5. Consistent Name Identification
The name used on the in-house label for the chemical to identify a chemical shall be the same as that used on the SDS and the manufacturer’s label. No abbreviations or chemical formulas may be used.
8.4.6. Exempt from Labeling Requirements of the OSHA Hazard Communication Standard
The following are exempt from the labeling requirements of the OSHA Hazard Communication Standard:
- Any pesticide defined in the Federal Insecticide, Fungicide, and Rodenticide Act when subject to the labeling requirements of that act and labeling regulations issued under that act by the EPA.
- Any chemical substance or mixture defined in the Toxic Substances Control Act when subject to the labeling requirements of that act and the labeling regulations issued under that act by the EPA.
- Any food, food additive, color additive, drug, cosmetic, or medical or veterinary device or product, including materials used as ingredients in such products (e.g., flavors and fragrances) defined in the federal Food, Drug, and Cosmetic Act or the Virus-Serum-Toxin Act of 1913 and regulated and subject to the labeling requirements under those acts by either the Food and Drug Administration or the Department of Agriculture.
- Any distilled spirits (beverage alcohols), wine, or malt beverage intended for nonindustrial use defined in the Federal Alcohol Administration Act and regulated and subject to the labeling requirements of that act by the Bureau of Alcohol, Tobacco, and Firearms.
- Any consumer product or hazardous substance defined in the Consumer Product Safety Act and Federal Hazardous Substances Act when subject to a consumer product safety standard or labeling requirements of those acts or regulations issued under those acts and regulated by the Consumer Product Safety Commission.
- Agricultural or vegetable seed treated with pesticides and labeled in accordance with the Federal Seed Act and regulated by the U.S. Department of Agriculture.
8.5 Safety Data Sheets (SDSs)
A master file of Safety Data Sheets (SDSs) containing the information required by the OSHA Hazard Communication Standard shall be kept by the purchaser and user for each substance in the work area. SDSs may be kept in any form, hard copy or electronic including operating procedures, and may be designed to cover groups of hazard chemicals in a work area where it may be more appropriate to address the hazards of a process rather than individual hazardous chemicals. The supervisor/principal investigator shall ensure that in all cases the required information is provided for each hazardous chemical and is readily accessible during each work shift to employees when they are in their work areas. SDSs shall be readily accessible to any employee at any time.
All SDSs shall contain the information specified in Table D.1 of 29 CFR 1910.1200 Appendix D. If no relevant information is found for any sub-heading within a section on the safety data sheet, the chemical manufacturer, importer or employer preparing the safety data sheet shall mark it to indicate that no applicable information was found. Sections 12-15 from the table may be included, but are not mandatory. No hazardous chemical is to be used without the corresponding SDS available in the work area. Units must not accept any hazardous chemical unless at least one of the following conditions is met:
- A Safety Data Sheet is provided with it,
- The manufacturer or vendor has been contacted to obtain the SDS,
- The SDS is available by electronic means in the work area, or
- The SDS is already on file in the work area.
Supervisory personnel and other users shall be responsible for maintaining an SDS for each hazardous chemical found/used in their respective work areas. It is recommended that paper copies of SDSs be kept in the work area, but electronic systems are also permitted. If SDSs are kept on an electronic system in the work area, the electronic system must be capable of providing a hard copy of the SDS without unreasonable delay, and all employees must be adequately trained by their supervisor/principal investigator to use the electronic system. In case of temporary power or equipment failure or other emergency, OEHS can be contacted to obtain SDSs from an online source. The SDS shall be the most current sheet supplied by the chemical manufacturer, importer, or distributor, or University employee evaluating the chemical hazard.
If supervisory personnel or others receive a new hazardous chemical for which they do not have an SDS in their work area, they shall contact manufacturer or vendor immediately to obtain a copy.
8.6 Information & Training Curriculum
The University shall provide employees with effective information and training on hazardous chemicals in their work area at the time of their initial assignment, and whenever a new chemical hazard the employees have not previously been trained on is introduced into their work area. Employees are obligated to learn and understand the hazards of the chemicals through reading the SDSs and chemical labels.
Information and training should be designed to cover categories of hazards (e.g., flammability, carcinogenicity) or specific chemicals. Chemical-specific information must always be available through labels and safety data sheets.
8.6.1. Employee Information
OEHS shall provide general training for supervisors/principal investigators, and/or DSRs in topics required by the OSHA Hazard Communication Standard. A brief introduction to the OSHA Hazard Communication Standard and a description of the University’s Hazard Communication Plan shall be provided to new employees during employee orientation.
Specific hazard communication training is the responsibility of the supervisor/principal investigator. Supervisors/principal investigators or their representatives shall use OEHS training as a guideline to be supplemented with on-the-job instruction specific to the work area. Supervisory training is required at the time of initial assignment and whenever a new physical or health hazard is introduced. As part of any training program for employees working with or potentially exposed to any hazardous chemicals, each employee must be provided the following information:
- Requirements of the OSHA Hazard Communication Standard.
- Knowledge of any operations in their work area where hazardous chemicals are present.
- The location and availability of the University’s written Hazard Communication Plan and chemical inventory.
- The location and availability of chemical SDSs.
8.6.2. Training
Training must be completed as expeditiously as possible and include the following:
- Methods and observations that may be used to detect the presence or release of hazardous chemicals in the work area (such as monitoring conducted by OEHS, continuous monitoring devices, visual appearance or odor of hazardous chemicals when being released, etc.)
- Knowledge of potential physical, health, simple asphyxiation, combustible dust, and pyrophoric gas hazards, as well as hazards not otherwise classified, of the chemicals in the work area.
- Measures employees can take to protect themselves from hazards, including specific procedures that the University has implemented to protect employees from exposure to hazardous chemicals such as engineering controls, appropriate work practices, emergency procedures, and personal protective equipment.
- Details of the Hazard Communication Plan, including an explanation of the labeling system, Safety Data Sheets, and how employees can obtain and use the appropriate hazard information.
Before any non-routine task is performed that could involve exposure to hazardous chemicals, the employee's supervisor/principal investigator must carefully review all potential hazards of the task with the employee and describe appropriate work practice procedures. Means of protection such as personal protective equipment or engineering controls must be provided where required and training must be documented by the supervisor/principal investigator.
Employees must be informed of hazardous chemicals in unlabeled pipes in their work area and of the potential hazards involved in the event of exposure to these substances (e.g., during maintenance operations). The extent of information provided shall include SDSs and other available information. The person or unit maintaining or using the pipe/pipe system is responsible for providing this information.
8.6.3. Training Resources
Training documentation is required (e.g., quizzes or employee interviews may be used) to verify that employees have understood the training and are able to demonstrate their understanding. If it is determined that employees lack an understanding of the potential chemical hazards in their areas and the means of protecting themselves, substantial fines could be imposed upon the supervisor/principal investigator or unit. Copies of training documentation must be sent to OEHS, or stored electronically if training is performed through an online training system.
8.7 Contractors
Contractors must have a hazard communication plan that will cover the methods of on-site access to safety data sheets, methods the employers (meaning both the University and the contractor) will use to inform the other employer of any precautionary measures that need to be taken to protect employees during the workplace’s normal operating conditions and in foreseeable emergencies, and methods the employer will use to inform the other employer of the labeling system used in the workplace. OEHS may rely on this plan instead of separate written documents, but only if these issues are addressed.
8.7.1. Contractor Hazard Information to the University
As part of the contractor’s hazardous communication plan to perform work at the University, the contractors must provide OEHS and the University employee responsible for the contractual agreement with a list of all hazardous chemicals that are to be used by the contractor’s employees working on University property and SDSs for each chemical. The contractor shall give an additional copy to the supervisor/principal investigator of the area. The supervisor/principal investigator shall then bear the responsibility for training University employees on the potential hazards of the chemicals to be used by the contractor. In addition, contractors must provide the following information to OEHS in writing, due before work begins:
- The methods the contractor will use to provide on-site access to SDSs for each hazardous chemical that their and University employees may be exposed to while working,
- The methods that the contractor will use to inform the University of any precautionary measures that need to be taken to protect employees during the workplace’s normal operating conditions and in foreseeable emergencies, and
- The methods the contractor will use to inform the University of the labeling system used in the workplace.
8.7.2. University Hazard Information to the Contractor
Contractors that may be exposed to hazardous chemicals in the workplace must be given the opportunity to review the University’s written Hazard Communication Plan and the Chemical Inventory for their contracted work area. Contractors bear the responsibility of training their employees on the potential hazards of each chemical. In addition, before work begins, OEHS and the University employee responsible for the contractual arrangement, with cooperation as necessary from the area supervisor/principal investigator or DSR, shall:
- Provide each contractor with an SDS for each hazardous chemical in the contracted work area. In turn the contractor shall inform OEHS in writing of their method used to provide the contractors employees on-site access to SDSs,
- Inform the contractor in writing of the methods the University shall use to inform the contractor of any precautionary measures that need to be taken to protect the contractor’s employees during the workplace’s normal operating conditions and in foreseeable emergencies, and
- And review the methods of labeling hazardous chemicals with the contractor. The contractor bears the burden of training their employees in the labeling system.
Upon request, OEHS shall assist Facilities Services or other units in gathering information for exchange with contractors.
8.8 Sealed Containers
In work operations where employees handle chemicals only in sealed containers that are not opened under normal conditions of use (such as in receiving), the following rules shall apply in order to be in compliance with the OSHA Hazard Communication Standard:
- Labels on incoming containers of hazardous chemicals must not be removed or defaced,
- Copies of SDSs that are received with incoming shipments of sealed containers of hazardous chemicals must be readily accessible to employees while in their work area. If a sealed container of a hazardous chemical is received without an SDS, the vendor or OEHS should be contacted, and
- OEHS shall provide information and training to supervisors who shall then ensure that employees under their supervision are provided the necessary training to protect themselves in the event of a spill or leak of a hazardous chemical from a sealed container.
8.9 Trade Secrets
The OSHA Hazard Communication Standard provides for the protection of trade secrets. Specific chemical identity may be withheld from an SDS by a manufacturer in some instances as long as:
- Information contained in the SDS concerning the properties and effects of the hazardous chemical is disclosed,
- The SDS indicates that the specific chemical identity and/or percentage of composition is being withheld as a trade secret, and
- The specific chemical identity and percentage is made available to health professionals, employees, and designated representatives in accordance with the applicable provisions of 29 CFR §1910.1200(i).
In the event of a medical emergency when immediate disclosure of the chemical identity is necessary for first aid or medical treatment, the trade secret must be divulged to health professionals, employees, and designated representatives. A written statement of need and a confidentiality agreement may be required by the manufacturer.
In non-emergencies, a health professional (i.e. physician, industrial hygienist, toxicologist, epidemiologist, or occupational health nurse) may request the disclosure of a specific chemical identity or percentage composition, if:
- The request is in writing,
- The request describes with reasonable detail one or more of the following occupational health needs for information:
o To assess the hazards of the chemicals to which employees will be exposed
o To conduct or assess sampling of the workplace atmosphere to determine employee exposure levels,
o To conduct pre-assignment or periodic medical surveillance of exposed employees,
o To provide medical treatment to exposed employees,
o To select or assess appropriate personal protective equipment for exposed employees,
o To design or assess engineering controls or other protective measures for exposed employees, and
o To conduct studies to determine the health effects of exposure.
-
The request explains in detail why the disclosure of the specific chemical identity or percentage is essential and that, in lieu thereof, the discloser of the following information to the health professional, employee, or designated representative, would not satisfy the purposes described above:
o The properties and effects of the chemical
o Measures for controlling workers’ exposure to the chemical,
o Methods of monitoring and analyzing worker exposure to the chemical, and
o Methods of diagnosing and treating harmful exposures to the chemical.
- The request includes a description of the procedures to be used to maintain the confidentiality of the disclosed information; and
- The health professional, OEHS or contractor of the services of the health professional (i.e. downstream employer, labor organization, or individual employee), employee, or designated representative, agree in a written confidentiality agreement that the health professional, employee, or designated representative, will not use the trade secret information for a purpose other than the health needs asserted and agreed not to release the information under any circumstances other than to OSHA, except as authorized by the terms of the agreement or by the chemical manufacturer or importer.
A chemical manufacturer or importer may deny the written request in writing within 30 days of the request; however, the denial must:
- Include evidence to support the claim that the specific chemical identity or percent of composition is a trade secret,
- State the specific reasons why the request is being denied, and,
- Explain in detail how alternative information may satisfy the specific medical or occupational health need without revealing the trade secret.
The health professional, employee, or designated representative whose request for information is denied may refer the request and the written denial of the request to OSHA for consideration.
Whether, because of a medical emergency or non-medical emergency, any employee needing the identity of a hazardous chemical that has trade secret protection should contact OEHS for assistance.
8.10 Laboratories
Although laboratories fall under the OSHA Laboratory Standard, the following rules of the OSHA Hazard Communication Standard shall also apply at the University:
- All containers of hazardous chemicals in laboratories must be labeled in accordance with the requirements set forth in this policy,
- Laboratories that ship hazardous chemicals must ensure that any containers of hazardous chemicals leaving the laboratory are labeled in accordance with the labeling policy set forth in this policy, and that an SDS(s) is provided along with the shipment. Laboratory employees must not remove or deface labels on incoming containers of hazardous chemicals,
- SDSs must be readily accessible to laboratory employees when they are in their work areas,
- Laboratory employees must be provided with information and training as described in this policy,
- Laboratories at the University must maintain a chemical inventory, and complete the Hazardous Chemicals Reporting review on an annual basis,
- A copy of the chemical inventory shall be available within the unit or on the job site for use by emergency response staff or agencies.
8.11 Referenced Regulations
- 29 CFR 1910.1200 Hazard Communication Standard
- 29 CFR 1910.1450 OSHA Laboratory Standard
- 29 CFR 1910.Subpart Z Toxic and Hazardous Substances
- 15 U.S.C. §2601 et seq. (1976) Toxic Substances Control Act
- Food, Drug, and Cosmetic Act (FD&C)
- Superfund Amendments and Reauthorization Act (SARA) of 1986
- Louisiana Hazardous Materials Information Development, Preparedness and Response Act 347
- Threshold Limit Values for Chemical Substances and Physical Reagents in the Work Environment published by the American Conference of Governmental Industrial Hygienists (ACGIH)
- Annual Report on Carcinogens published by the National Toxicology Program (NTP)
- Monographs published by the International Agency for Research on Cancer (IARC)
- GHS (Rev.6)(2015) Globally Harmonized System of Classification and Labelling of Chemicals
Consequence of Violating the Policy
Violation of this policy may result in disciplinary action, up to and including termination. For consequences of violating the policy refer to the Faculty and Staff handbooks found at policy.tulane.edu